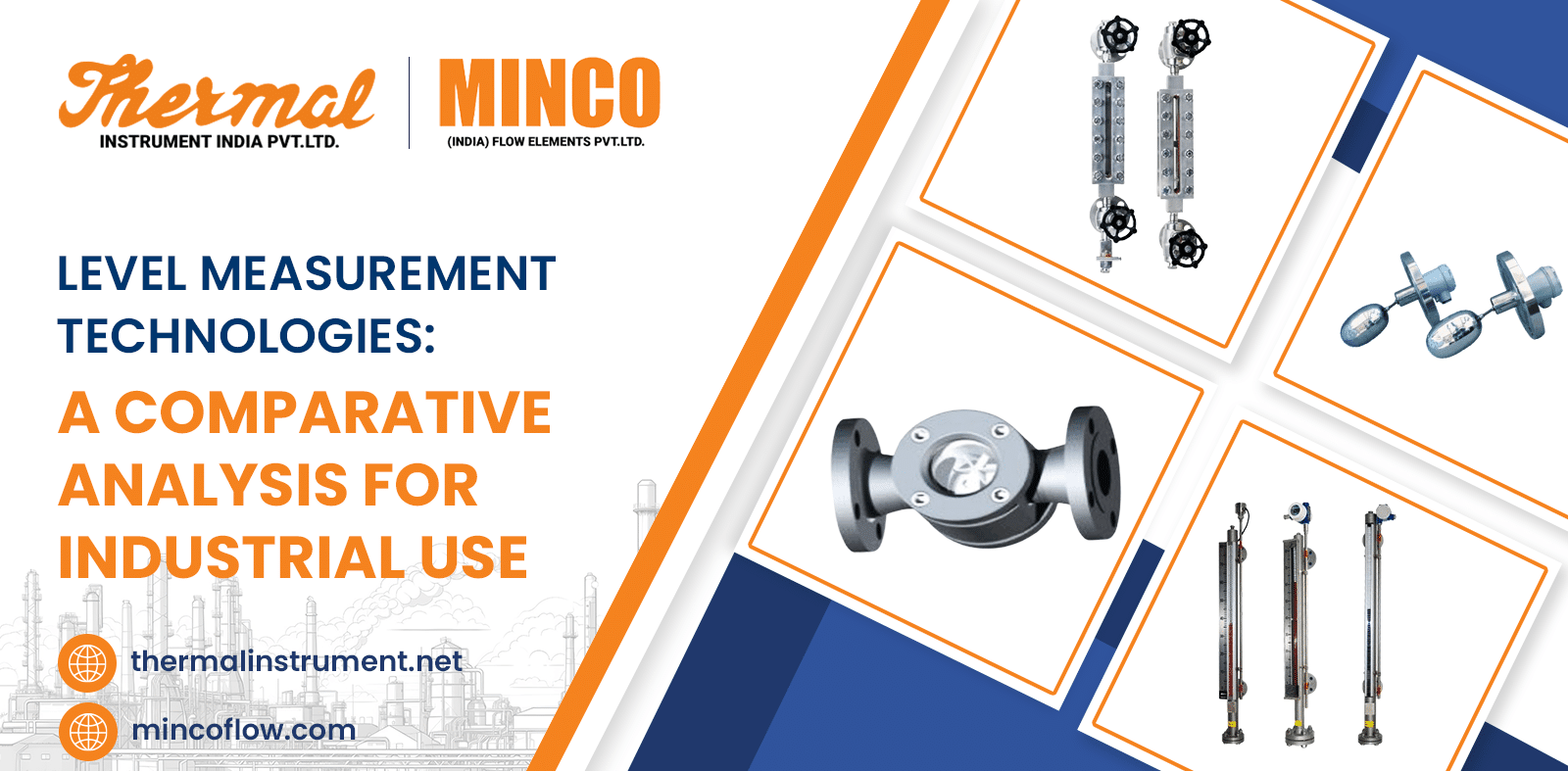
Level Measurement Technologies: A Comparative Analysis for Industrial Use
Accurate liquid level measurement is crucial for industrial processes, ensuring efficiency, safety, and compliance. At Thermal Instrument, we offer a variety of advanced technologies to meet diverse industrial needs. Selecting the right solution depends on factors such as fluid characteristics, operating conditions, and application requirements. In this blog, we’ll compare key level measurement technologies, including Level Switches, Liquid Level Gauges, Reflex Gauges, Tubular Gauges, Magnetic Gauges, Level Transmitters, Flow Switches, and Sight Flow Indicators.
Level switches detect the presence of liquid at specific points, providing simple on/off control and alarms for high and low levels.
Best For: Point-level detection
Applications: Tanks, reservoirs
Benefits: Low-cost, easy installation, minimal maintenance
Visual indicators that show liquid levels in a tank, suitable for applications where precision is secondary to simplicity.
Best For: Visual indication
Applications: Water treatment, chemical storage
Benefits: Simple, durable, low-tech
These gauges use light refraction to indicate liquid levels and are ideal for distinguishing liquid and gas phases.
Best For: Water and steam levels
Applications: Boilers, high-pressure tanks
Benefits: Clear readability, durable
Transparent tubes attached to tanks provide a simple visual reading, suitable for low-pressure environments.
Best For: Basic applications
Applications: Open tanks, chemical storage
Benefits: Affordable, easy to install
Magnetic level gauges offer precise, continuous level measurement using a float and magnetic follower, ideal for extreme conditions.
Best For: Hazardous environments
Applications: Refineries, power plants
Benefits: No direct fluid contact, reliable in high pressure/temperature
Transmitting real-time liquid levels, these devices offer high accuracy and are perfect for automation.
Types: Radar, Ultrasonic, Differential Pressure
Best For: Continuous measurement
Applications: Process control, large tanks
Benefits: High precision, remote monitoring
These devices monitor liquid flow, ensuring proper flow rates and preventing equipment damage.
Best For: Flow monitoring
Applications: Cooling systems, HVAC
Benefits: Real-time monitoring, equipment protection
Sight flow indicators provide visual confirmation of fluid flow in pipelines and are used for low-pressure processes.
Best For: Visual flow monitoring
Applications: Food processing, pharmaceuticals
Benefits: Simple, low-cost, easy to maintain
Choosing the Right Technology
When choosing the right level measurement technology, various factors come into play:
Process fluid characteristics: Viscosity, toxicity, corrosiveness, and pressure
Operating environment: Temperature extremes, outdoor vs. indoor use, and safety requirements
Level measurement type: Continuous or point level
Installation and maintenance requirements: Complexity, ease of access, and cleaning needs
Conclusion
Selecting the right level measurement technology depends on your application’s specific needs, such as fluid type, pressure, and accuracy. Thermal Instrument offers a comprehensive range of level measurement solutions, from simple level switches to advanced magnetic gauges and transmitters. With over 50 years of industry expertise, we provide reliable, durable solutions for even the most challenging environments.
Ready to elevate your process control? Discover cutting-edge level measurement technologies tailored to your industrial needs. Reach out here now for expert guidance and solutions!